When utilizing heavy machinery and industrial equipment, the entire operation can go down the drain if hydraulic hoses fail. Hydraulic systems play an extremely vital role since they ensure the transmission of hydraulic fluid and, consequently, power.
This comprehensive guide will delve into the role hydraulic hoses play in heavy machinery and equipment. Additionally, we will explore best practices for their maintenance and examine common failures that may occur. But first, let us start with the basics—what exactly are hydraulic hoses, and what are they composed of?
Understanding Hydraulic Hoses
Hydraulic hoses are specialized tubes designed to convey hydraulic fluid under pressure in hydraulic systems. These hoses are engineered to withstand high pressures and temperatures while maintaining flexibility, making them a vital part of heavy machinery. Their primary function is to transmit hydraulic power from one component to another, enabling the machinery to perform various tasks, such as lifting, pushing, pulling, and rotating.
Hydraulic Hose Components
Hydraulic hoses are composed of several key components that work together to ensure durability and efficiency under demanding conditions. These components include:
- Inner Tube: The inner tube is the innermost layer of the hydraulic hose, responsible for carrying the hydraulic fluid. It is typically made from synthetic rubber or thermoplastic material, chosen for its compatibility with the specific hydraulic fluid used and its ability to resist wear and tear.
- Reinforcement Layer: Surrounding the inner tube is the reinforcement layer, which provides the hose with its strength and flexibility. This layer is usually constructed from braided or spiral-wound wire or textile materials, designed to withstand high-pressure conditions.
- Outer Cover: The outer cover is the protective layer that shields the inner components from external elements such as abrasion, chemicals, and environmental factors. It is typically made from synthetic rubber or thermoplastic material with properties that resist aging and damage.
Each of these components is critical for the overall performance of the hydraulic hose. The inner tube must be compatible with the hydraulic fluid to prevent degradation, the reinforcement layer must provide sufficient strength to handle high pressures, and the outer cover must protect the hose from external damage.
Common Hydraulic Hose Failures
Hydraulic hoses are susceptible to wear and failure over time. Identifying and understanding the common causes of hydraulic hose failures can help in preventing unexpected breakdowns and prolong the life of the equipment. Some of the top reasons for hydraulic hose failures include:
- Abrasion: One of the most common causes of hydraulic hose failure is abrasion. Constant contact with other components or surfaces can wear down the outer cover, exposing the reinforcement layer and inner tube to potential damage.
- Improper Installation: Incorrect installation of hydraulic hoses can lead to premature failure. Issues such as excessive bending, twisting, or incorrect routing can cause stress on the hose, leading to leaks or bursts.
- Incompatible Fluids: Using hydraulic fluid that is not compatible with the hose material can cause the inner tube to degrade, leading to leaks and reduced performance.
- Aging and Weathering: Over time, exposure to environmental factors such as UV radiation, extreme temperatures, and chemicals can cause the hose material to deteriorate, resulting in cracks and leaks.
- Pressure Surges: Sudden spikes in hydraulic pressure, known as pressure surges, can exceed the hose's rated capacity, causing it to burst or develop leaks.
The impact of hydraulic hose failures on heavy machinery operations can be significant. Downtime due to hose failures not only leads to lost productivity but also increases maintenance costs and poses safety risks to operators and equipment.
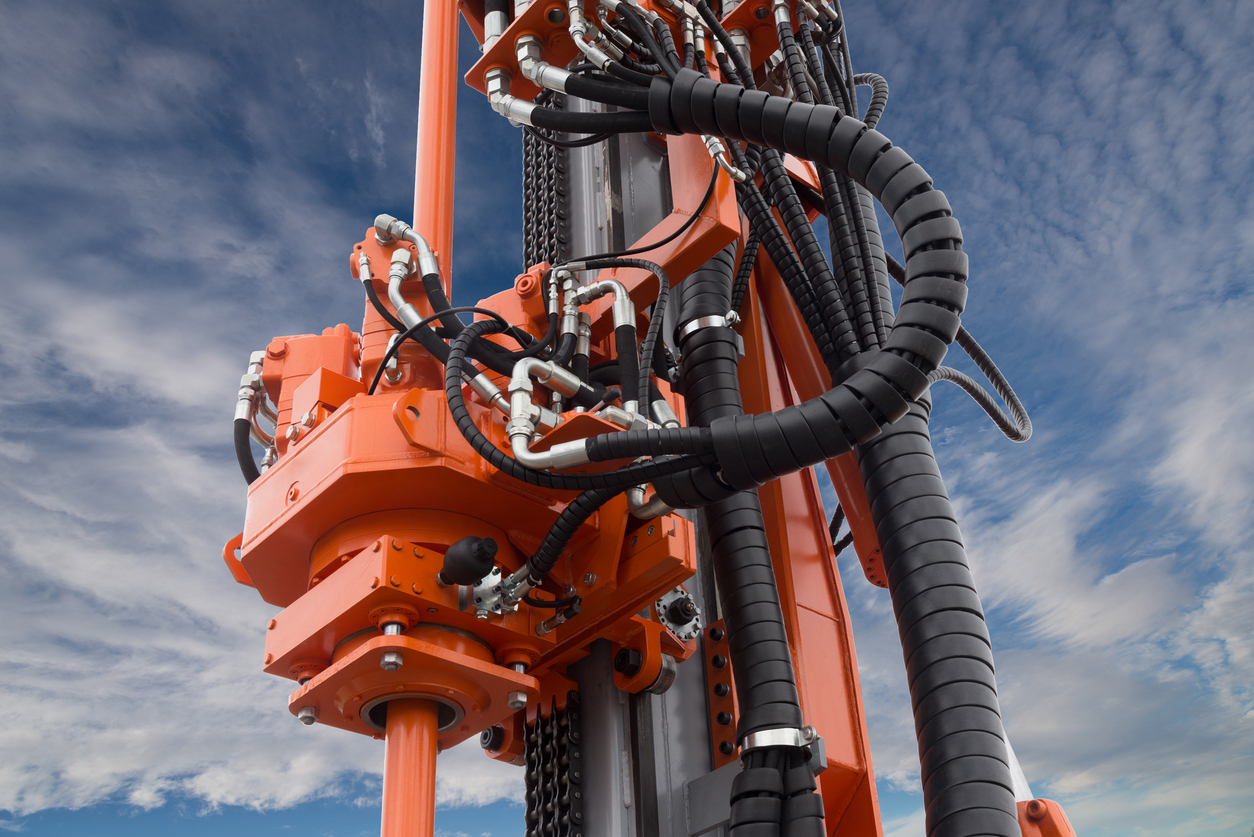
Best Practices for Hydraulic Hose Maintenance
Regular inspection and maintenance of hydraulic hoses are essential to prevent failures and ensure optimal performance. Here are some best practices for maintaining hydraulic hoses:
- Regular Inspection: Conduct routine inspections to check for signs of wear, damage, and leaks. Pay close attention to areas where the hose may be subjected to abrasion or excessive bending.
- Proper Storage: Store hydraulic hoses in a cool, dry, and clean environment, away from direct sunlight and chemicals. Proper storage helps prevent premature aging and damage.
- Correct Installation: Follow manufacturer guidelines for proper installation, including correct routing, bending, and securing of the hoses. Avoid excessive twisting and bending that can cause stress on the hose.
- Fluid Compatibility: Ensure that the hydraulic fluid used is compatible with the hose material to prevent degradation of the inner tube.
- Pressure Management: Monitor and regulate hydraulic pressure to avoid pressure surges that can exceed the hose's rated capacity.
- Replace Worn Hoses: Replace hoses that show signs of wear, damage, or degradation promptly to prevent unexpected failures.
Benefits of Proactive Hydraulic Hose Maintenance
Implementing proactive maintenance practices for hydraulic hoses offers several benefits, including:
- Reduced Downtime: Regular inspection and maintenance help identify potential issues before they lead to failures, reducing unexpected downtime and keeping machinery operational.
- Lower Operational Costs: Preventive maintenance reduces the need for costly emergency repairs and replacements, leading to overall lower operational costs.
- Enhanced Safety: Well-maintained hydraulic hoses reduce the risk of leaks and bursts, enhancing the safety of operators and equipment.
- Improved Performance: Properly maintained hoses ensure consistent hydraulic power transmission, improving the performance and efficiency of the machinery.
Let’s Review
Hydraulic hoses are a critical component of heavy machinery and equipment, serving as the conduit for hydraulic power transmission.
For any serious business, investing time and resources to replace and maintain hydraulic hoses makes good business sense. It keeps things running smoothly and ensuring optimum performance helps to reduce costly downtime, therefore maintaining your equipment in top condition, for longer.
If you have any questions our guide did not cover, feel free to contact us.