Choosing the correct pipes and valves for industrial systems is necessary to ensure efficacy, safety, and longevity. The decision process can become complicated due to the diverse needs of each industry, whether it is in the petrochemical, water treatment, or manufacturing fields. With that in mind, we have put together a guide that will help you walk through the important steps and considerations to help you make informed decisions.
Understanding Industrial Needs
Different industries have unique requirements when it comes to piping and valve systems. Understanding these requirements is the first step in making the right choices.
Petrochemical Industry
In the petrochemical sector, pipes and valves must withstand harsh chemicals, high pressures, and extreme temperatures. Corrosion resistance and material compatibility are paramount to prevent leaks and ensure safety.
Water Treatment Industry
Water treatment facilities require pipes and valves that can handle varying pressures and temperatures while resisting corrosion caused by water and chemicals used in the treatment process. Longevity and ease of maintenance are critical factors.
Manufacturing Industry
Manufacturing plants often deal with diverse materials and processes, needing a versatile and robust piping system. Valves and pipes must be adaptable to different media, including gases, liquids, and slurries, and be able to function efficiently under varying operational conditions.
Types of Pipes and Valves
Pipes
- Steel Pipes: Known for their strength and durability, steel pipes are ideal for high-pressure applications. Stainless steel offers excellent corrosion resistance, making it suitable for harsh environments.
- PVC Pipes: Lightweight and resistant to chemicals, PVC pipes are commonly used in water treatment and chemical processing industries.
- Copper Pipes: Offering superior thermal conductivity, copper pipes are often used in systems requiring efficient heat exchange.
Valves
- Gate Valves: These are used to start or stop the flow of liquid. They are not suitable for regulating flow but are excellent for applications where the flow needs to be fully open or fully closed.
- Ball Valves: Offering reliable sealing and low-pressure drop, ball valves are suitable for applications requiring tight shutoff.
- Butterfly Valves: Known for their compact design and quick operation, butterfly valves are used in large volume water applications and are ideal for throttling purposes.
Factors to Consider
When selecting pipes and valves for industrial use, several factors must be cautiously analyzed to ensure optimal performance.
Pressure
Understanding the pressure requirements of your system is crucial. Pipes and valves must be rated for the maximum pressure they will encounter to avoid failures.
Temperature
Temperature ratings are equally important. High temperatures can weaken materials, while low temperatures may cause brittleness. Make sure the materials chosen can handle the temperature ranges of your application.
Fluid Compatibility
The media flowing through the pipes and valves—whether it be gas, liquid, or slurry—must be compatible with the materials of construction to avoid corrosion and degradation.
End Connections
The type of end connections (flanged, threaded, welded) should match the existing piping system to ensure seamless integration and prevent leaks.
Delivery Requirement
Consider the lead times and delivery requirements. It is essential to work with suppliers who can meet your schedule and provide consistent quality.
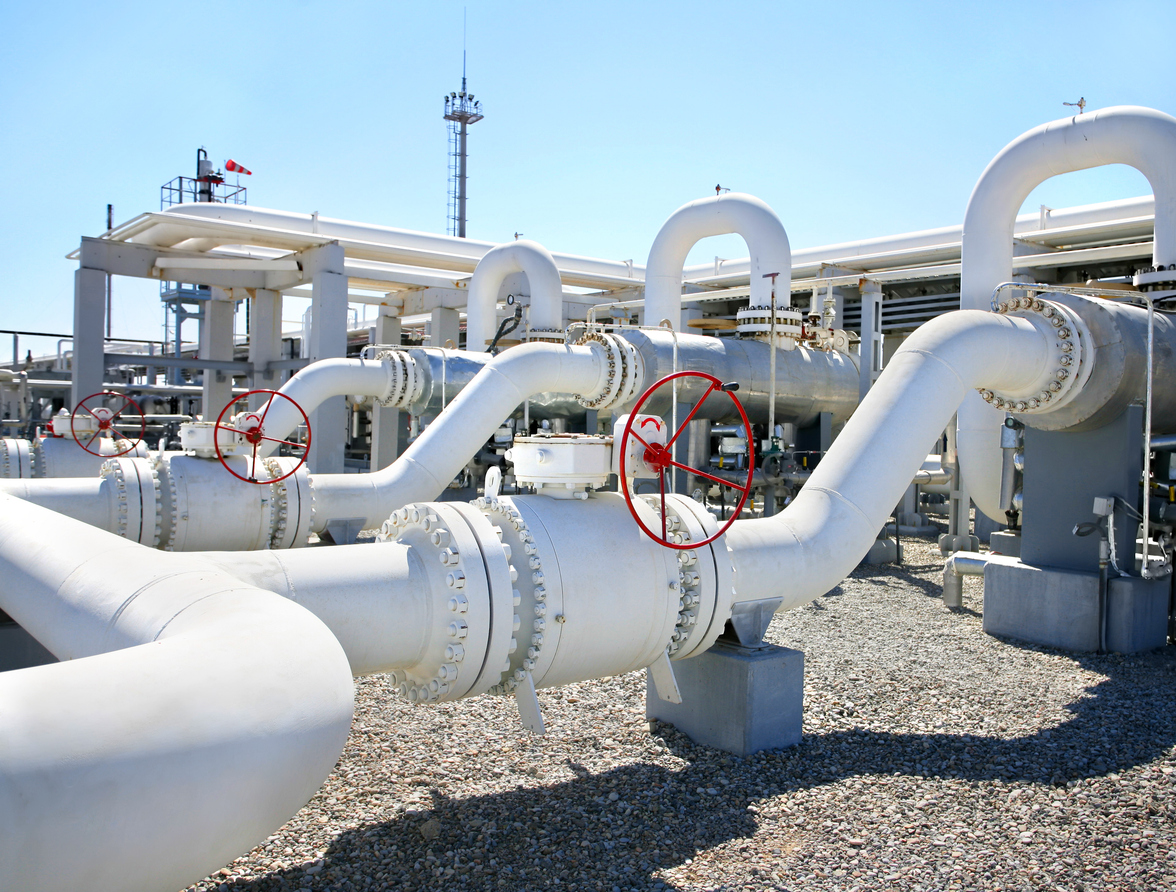
The STAMPED Method
The STAMPED method is a systematic approach to selecting the correct pipes and valves for any industrial application. It ensures that all critical factors are considered.
S - Size
Ensure the pipe and valve sizes meet the flow requirements of your system. Oversized or undersized components can lead to inefficiencies and potential damage.
T - Temperature
Confirm that the selected materials can withstand the operational temperatures without compromising integrity.
A - Application
Understand the specific application and environment in which the pipes and valves will be used to select materials and designs that offer optimal performance.
M - Material/Media
Consider the type of media that will flow through the system. Ensure that the materials are compatible to prevent chemical reactions that could lead to failure.
P - Pressure
Select components that can handle the maximum pressure the system will experience. Over-specifying can increase costs, while under-specifying can lead to system failures.
E - End Connections
Ensure that the end connections match your system's requirements to facilitate easy installation and maintenance.
D - Delivery Requirement
Plan according to your project timelines and ensure that the chosen supplier can meet your delivery needs without compromising on quality.
Quality and Compliance
Importance of High-Quality Components
Using high-quality pipes and valves is non-negotiable in industrial applications. Poor quality components can lead to system failures, safety hazards, and costly downtime. Always opt for suppliers who adhere to stringent quality control processes and industry standards.
Industry Standards
Make sure that the selected pipes and valves comply with relevant industry standards and certifications. This guarantees reliability, safety, and performance. Standards such as ASTM, ANSI, and ISO provide guidelines for material specifications, dimensions, and testing procedures.
Selection Process
Step-by-Step Guide
- Assess Your Needs: Conduct a thorough assessment of your system's requirements, including pressure, temperature, and media compatibility.
- Research and Compare: Research different materials and types of pipes and valves. Compare their properties and suitability for your application.
- Consult Experts: Engage with industry experts or consultants who can provide insights and recommendations based on your specific needs.
- Evaluate Suppliers: Choose reputable suppliers known for their quality and compliance with industry standards.
- Install and Test: Once selected, ensure proper installation by qualified personnel. Conduct rigorous testing to verify the performance of the pipes and valves under operational conditions.
- Regular Maintenance: Implement a regular maintenance schedule to ensure the longevity and reliability of your piping system.
Wrapping Up
Deciding upon the right pipes and valves for industrial applications is a critical task that requires careful consideration of various factors. By understanding your specific needs, using the STAMPED method, and prioritizing quality and compliance, you can ensure the efficiency, safety, and durability of your system. If you have any questions that our article did not cover, please do not hesitate to contact us.